How to replace the Valve Body on a 09G transmission for VW and MINIs. Automatic Transmission Valve Body 6-Speed 09G325039A AW 09G TF-60SN 09G valve body For Audi VW Jetta Golf Passat Touran Sharan 03-up 2003-2011 2.0 out of 5 stars 1 $360.00 $ 360. ATSG 09G Transmission Repair & Rebuild Manual Book TF60SN VW Mini Audi 6 Speed. Seller 100% positive. 1958 Chevrolet Corvette Assembly Manual Book. Sonnax transmission products are the number one choice of large transmission remanufacturers, quality valve body rebuilders, and veteran independent specialists around the world. To better meet the repair challenges of increasingly sophisticated modern transmissions, Sonnax also offers premium remanufactured valve bodies.
AUDI, JETTA, PASSAT, 09G/09M – ATSG PDF. This manual contains the procedures necessary to diagnose, rebuild and/or repair the 09G/09M transaxle and is intended for automotive technicians that are familiar with the operation of automatic transmissions.
Transaxle, which is a 6 speed, fully automatic and electronic controlled transaxle. Volkswagen engineers were also involved, in conjunction with Aisin, in the development process for their vehicles and they gave it the 09G/09M designation. BMW gave it the designation 6F21WA for their Mini-Cooper.
The 09G/09M transaxle is used in a wide variety of applications and engine sizes. As a result, the number of friction plates, planetary ratios, intermediate ratios and final drive ratios will vary depending on torque load requirements of the specific vehicle. The TF60SN transaxle uses a gear ratio sensitive system, requiring the correct transaxle interchange. The TF60-SN is used in the BMW Mini Cooper, Volkswagen and Audi vehicles.
This transaxle is referred to as the TF60-SN, 09G, 09M, 6F21WA and in some overseas vehicles as 09K. As a result there are a variety of different case and part configurations. Some of these units have the heat exchanger attached to the transmission while others use a remote heat exchanger. This alters the case, case cover and the valve body and if incorrect parts are used, severe planetary failure will occur. This manual covers these differences so that this mistake will not happen to you.
The 09G/09M transaxle uses a Lepelletier arrangement, using a simple planetary coupled with a Ravigneaux planetary. This arrangement makes six forward speeds and reverse possible, with only five clutch packs and one freewheel.
- Volkswagen Transporter T5
- 2007 Volkswagen Jetta, US market
- 2009 Volkswagen Tiguan, US market
- various Seat, Skoda, Audi models
CONTENTS
- GENERAL DESCRIPTION AND VEHICLE APPLICATION CHART
- COMPONENT APPLICATION CHART
- IDENTIFICATION TAG LOCATION AND INFORMATION
- SPEED SENSOR INFORMATION
- PRESSURE SWITCH AND FLUID TEMPERATURE SENSOR INFORMATION
- SOLENOID LOCATIONS AND IDENTIFICATION
- INDIVIDUAL SOLENOID FUNCTION AND FAILURE RESULT
- SOLENOID OPERATION
- SOLENOID APPLICATION CHART
- PASS-THRU CASE CONNECTORS AND WIRE HARNESS
- CASE CONNECTOR TERMINAL IDENTIFICATION
- CASE CONNECTOR INTERNAL COMPONENT RESISTANCE CHARTS
- TCM CONNECTOR INTERNAL COMPONENT RESISTANCE CHARTS
- TRANSAXLE RANGE SWITCH OPERATION AND DIAGNOSIS
- STANDARD AND TIPTRONIC SHIFT QUADRANTS
- TYPICAL WIRE SCHEMATIC
- DIAGNOSTIC TROUBLE CODE DESCRIPTION
- TORQUE CONVERTER CLUTCH OPERATION
- PRESSURE TAP LOCATIONS AND IDENTIFICATION
- PRESSURE SPECIFICATIONS
- TRANSAXLE OIL COOLER INFORMATION
- OIL PASSAGE IDENTIFICATION
- CHECK FLUID LEVEL AND FLUID REQUIREMENTS
- OIL PAN “STAND-PIPE” DIFFERENCES
- OIL PAN AND OIL PAN GASKET DIFFERENCES
- OIL FILTER DIFFERENCES
- TRANSAXLE DISASSEMBLY
- COMPONENT REBUILD
- CONVERTER COVER ASSEMBLY
- TRANSAXLE CASE ASSEMBLY
- OIL PUMP ASSEMBLY
- K3 CLUTCH HOUSING ASSEMBLY
- K1 CLUTCH HOUSING ASSEMBLY
- K2 CLUTCH HOUSING ASSEMBLY
- REAR PLANETARY ASSEMBLY
- FRONT PLANETARY ASSEMBLY
- CENTER SUPPORT ASSEMBLY
- TRANSFER DRIVEN GEAR AND FINAL DRIVE ASSEMBLY
- VALVE BODY ASSEMBLY
- TRANSAXLE FINAL ASSEMBLY
- B2 CLUTCH CLEARANCE MEASUREMENT
- F1 ROLLER CLUTCH FREEWHEEL DIRECTION
- B1 CLUTCH CLEARANCE MEASUREMENT
- TRANSAXLE END-PLAY MEASUREMENT
- CONVERTER INSTALLED MEASUREMENT
- THRUST WASHER AND BEARING IDENTIFICATION
- TORQUE SPECIFICATIONS
- “UPDATED” TRANSAXLE CODE INFORMATION
Language: English
Format: PDF
Pages: 124
The Aisin-Warner 09G six speed FWD transmission, or TF-60, has increased in popularity and technicians need to become more familiar with all aspects. The 09G can be found in a variety of Volkswagen FWD vehicle platforms produced after 2003. Its close cousins, the TF80 (Volvo and GM) and TF81 (Ford and Mazda) further enhance a huge market potential for the transmission repair industry.
Much focus has been spent over the years on valvebody wear issues and other deficiencies of the 09G as well as the TF80 / TF81 models. Once a repair had been made, shift or apply issues still existed at times requiring more attention to the controls.
The experts at Rostra have devoted a substantial amount of effort to determine how all of the aspects of Aisin 6-speed transmissions (valvebody, solenoids, and TCM) work together to provide a good functioning and durable transmission repair.
The following is a summary of that research:
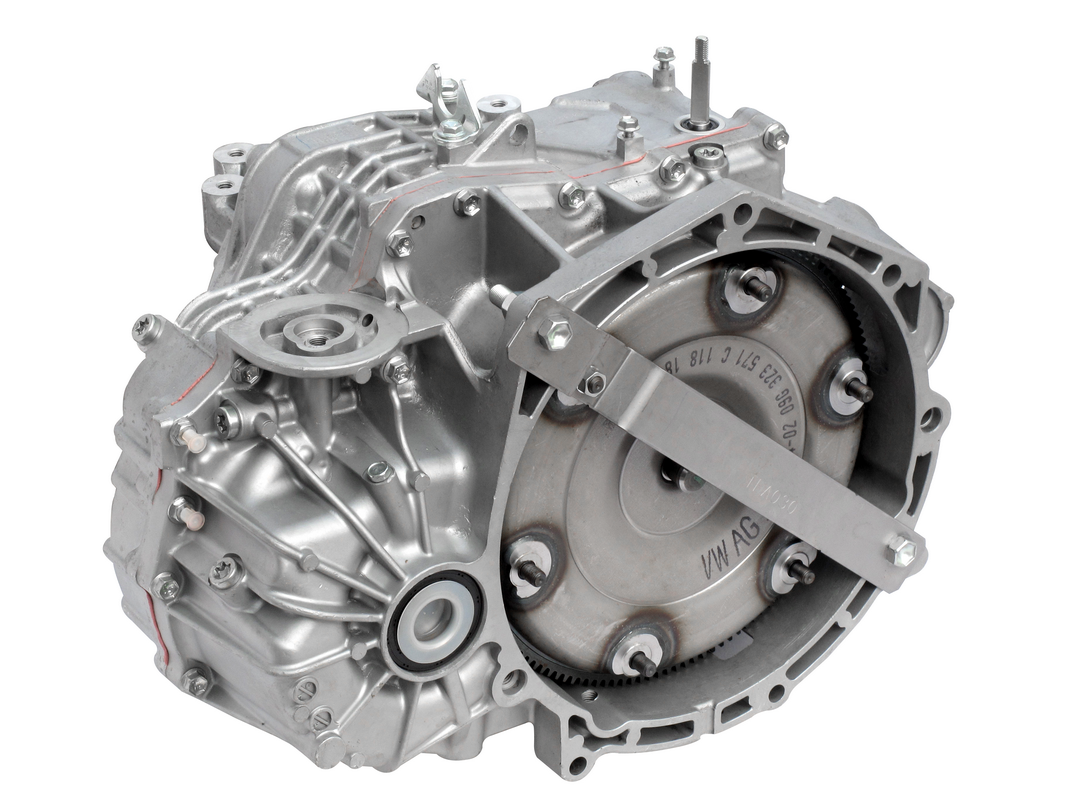
09g Transmission Rebuild
Aisin-Warner has made several improvements related to the operation and design of this 6-speed family relative to earlier 5-speed (AW55-50) family, including the utilization of dedicated linear solenoids to directly control clutches. With this improved system, the TCM has more ability to adapt and precisely control the quality of shifts but ultimately the control is limited. Whenever any conditions change within the hydraulic circuit, such as the valvebody or solenoids, adjustments to the system may be necessary. This article will dissect exactly what is happening during select shifts and how to make adjustments to the valvebody in order to obtain the desired level of drivability. The 09G will be the specific focus of the article although most of the information holds true for the 09D (TR60), TF80, and TF81.
First, let’s examine the solenoids and their role in the transmission. The 09G has six linear solenoids and two on/off solenoids. Of the six linear solenoids, four of the units directly control clutches and brakes via spring loaded spool valves in the valvebody. The remaining two control line pressure and torque converter lock-up. Five of the linear solenoids are normally open and function to reduce pressure output with increased current draw. The TCC solenoid is normally closed and increases pressure output with increased current draw. The two on/off solenoids are normally closed and are energized for various purposes including engine braking and torque converter lock-up. The detailed function of each solenoid and clutch is illustrated in Figure 1.
Vw 09g Transmission Problems
Figure 109G Solenoid and Component Chart
Operation of Solenoids During Shifts
To understand how the linear solenoids control the engagement of the clutches and brakes, we must first understand the signal driving them. The linear solenoids are supplied 12V power in the form of a 300 Hz PWM signal. An accepted but ineffective aftermarket industry standard is to simply measure current being supplied to the solenoids to determine load. Due to the variations in current draw depending on heat and specific resistance of the solenoid, measuring duty cycle percentage is a more consistent, accurate, and preferred representation of solenoid load. The solenoids are driven by signals that vary from 12-60% duty cycle with 60% being “fully energized,” limiting the normally open solenoid’s output to near 0 psi. At 12% duty cycle the solenoid is essentially “off” which allows all input pressure to pass through a normally open solenoid. The majority of pressure modulation occurs between 20 and 55% duty cycle. Figure 2 below shows the signals applied to K1, K2, and K3 control solenoids on the tail-end of a 3-4 shift where the duty cycles are 12%, 40% and 60% respectively. As a reference, the time elapsed between each peak is 3.33 milliseconds.
Figure 2Raw Signal Data from 09G
Electronic control over the entire pressure range of the transmission means that the TCM can ramp the rise and drop of pressure to specific clutches and brakes in order to achieve a smooth shift. Most shifts are comprised of one clutch (or brake) being applied and another clutch (or brake) is being released (synchronous shift). In an ideal shift situation, the two components will have minimal time between application of the two components. Figure 3 illustrates how the signals and pressures are being modulated in the same 3-4 shift as featured in Figure 2. Figure 3 shows that during the 3-4 upshift the K2 clutch is applying and the K3 clutch is releasing. Notice how K3 control solenoid ramps up the signal to inversely drop the pressure in the K3 circuit while at the same time, the opposite occurs for the K2 solenoid signal and hydraulic circuit. Application pressures for the K2 and K3 clutches are near 30 psi indicating that for approximately 100 ms, neither the K2 nor K3 clutch was engaged. If the time between clutch applications was longer (over 1⁄4 second) the RPMs would begin to rise as if in neutral then drop quickly resulting in a shift flare then bump. On the other hand, if the K2 clutch is applied before K3 releases; the transmission is effectively trying to temporarily operate at two different gears simultaneously resulting in a bind-up.

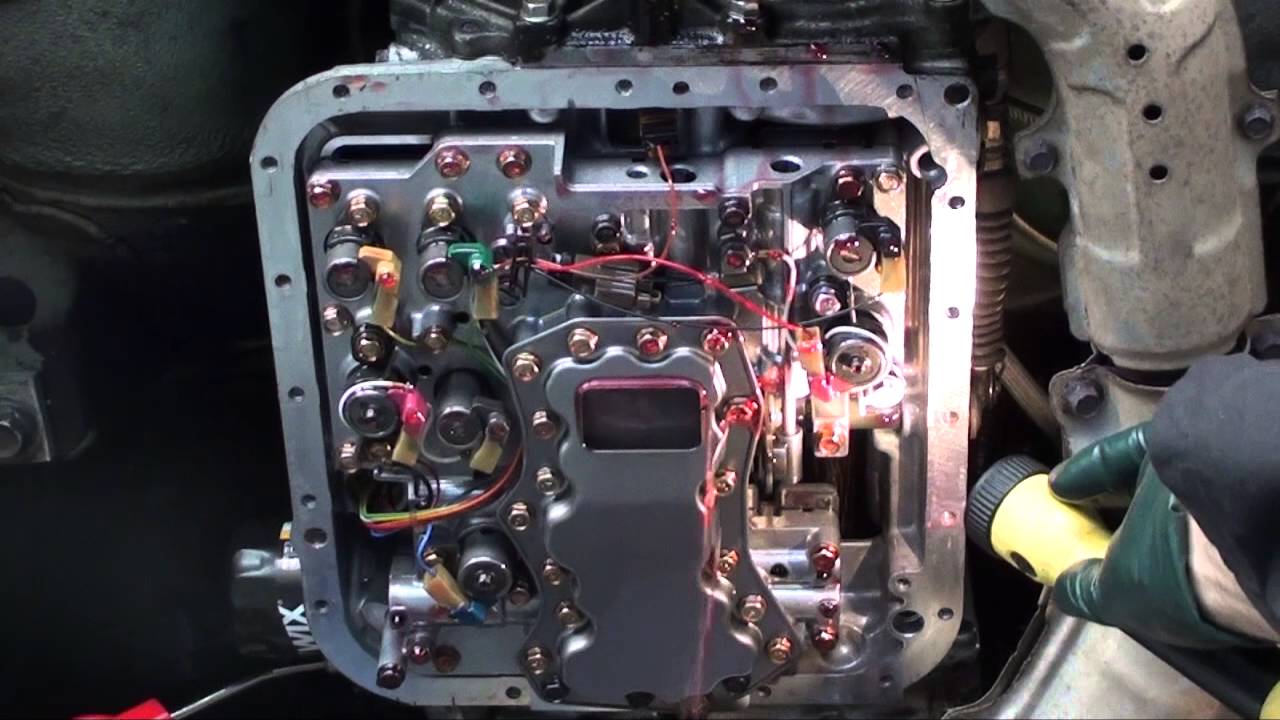
Figure 3Signals and Pressure 3-4 Shift
Relearn and Calibration
Unlike the solenoids in the AW55 transmission, the AW 6 solenoids are not adjustable. Aisin-Warner has elected to compensate for the variations in solenoid output by implementing adjustment screws directly on the valvebody. Calibration of the valvebody with solenoids installed as a whole system is necessary to ensure a consistent quality of shifts. In the event that any clutch’s control system output relative to drive signal changes, shift quality and drivability may suffer resulting in flares or bind-ups. Poor shift performance could be caused by simply replacing solenoids with different preset calibrations or repairing the valvebody to fix leaks which the TCM has already taken into account. In most situations the TCM is capable of adjusting the drive signals to smooth out any harsh shifts. Through normal driving, this may be a slow and tedious process requiring up to 50 miles of drive time. To help accelerate this process, it is recommended that the shop perform a relearn procedure:
- With the transmission at normal operating temperature and no codes present, shift from Park to Reverse to Neutral to Drive and back, staying in each range for 10 seconds. Repeat this at least 5 times.
- Accelerate through the first 5 gears under light throttle (10%) then come to a stop. Repeat this 5 times.
- Accelerate through all gears at medium throttle (50%) then come to a stop. Repeat this 5 times.
- Manually downshift through all gears. Repeat this 5 times.
09g Transmission Fluid
It’s important to remember that the intent of the relearn procedure is to simulate many miles of average driving in a short time. If there is one particular shift that is harsh, it would be beneficial to repeat that shift with greater frequency.
After performing this relearn procedure, it is still possible for the hydraulics to be so far from the system’s norm that manual calibration of the valvebody is necessary to achieve the desired drivability. The first step in calibrating a valvebody is to identify which clutch or brake control needs to be adjusted. Figure 4 below illustrates common drivability issues and the appropriate clutch and brake control to adjust in order to resolve the issue. For example, if a vehicle was experiencing a flare on the 3-4 shift, the resolution would be to turn the adjustment screw on the spring tensioner for the spool valve that shares the bore with the K2 control solenoid in the counter-clockwise direction. One complete turn of the screw can resolve a slight application issue while an obvious flare or bind-up may be resolved by two complete rotations of the screw.
Figure 4Clutch and Brake Controller Adjustment Chart
09g Transmission Problems
The engagement into Drive and Reverse can be particularly tricky to diagnose whether the pressure is too high or low. In Figure 5, the effects of both and high and low K3 pressures can be seen on the engagement of reverse. In an ideal clutch application, the pressure gradually rises to 30 psi as seen in the Smooth Engagement. If the pressure rise is too sudden, the engagement will be harsh. Notice how the early engagement reaches the engagement pressure before the ramp sequence while the delayed engagement finishes the ramp sequence before it reaches the engagement pressure. The harshness of both the early and delayed engagement featured in Figure 5 could be perceived to be of the same magnitude. When diagnosing the difference between high and low pressure, it is important to focus on the time between moving the gear selector and the bump that follows. The early engagement will happen almost instantaneously whereas the delayed engagement will take up to 2 seconds to feel the bump.
Figure 5Delayed, Smooth and Early Reverse Engagements
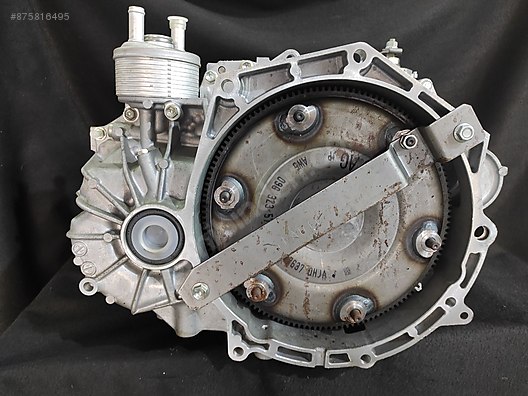
The line pressure circuit and EPC solenoid do not have adjustment screws and all of their corrections are relegated to the TCM. The TCC solenoid does have an adjustment screw that is typically staked and nonadjustable. Similarly, TCC corrections can only be made by the TCM. It should be noted that if the output pressure is lower than normal in the TCC solenoid, the initial torque converter lock-up engagement while in third gear could be firm and feel similar to a 3-4 shift. When diagnosing it is important to confirm which gear is engaged by using a scan tool or the Tiptronic system of the vehicle. Shift firmness should work itself out through the relearn procedure.
The improved design of the hydraulic control system in the 09G allows you to take the guess work out of resolving drivability issues. Direct control of the clutch and brake components through dedicated solenoids, along with the ability to adjust pressures of the hydraulic circuits, make diagnosis and resolution of drivability issues more of a science and less of an art.
Currently, OEM solenoids are only available by purchasing an entire valvebody. Rostra however, has linear solenoids available and with an improved design. Problems with OE solenoids involve wear or debris build up affecting the internal bushings. Rostra has redesigned the bushings to prevent those issues such as wear or sticking of the spool valve. The solenoid body has also been redesigned for better oil flow. The on-off solenoids are under development as well. Contact Rostra Powertrain or Rostra distributors for a complete listing of Aisin solenoids as well as other Rostra products.
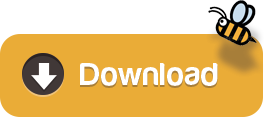